Risks of Reroofing with a Metal Roof
When considering whether or not to reroof over a commercial metal roof, there are certain risks that must be taken into account. At ACR1, we’ve put together a guide on common metal roofing problems and how they can be handled.
Leaks
Leaks through a metal roof can be caused by a number of factors such as driving rain, melted or heavy snowfall, wind, structural damage, severe weather, ice damming, etc. Leaks can also be caused by installation errors such as failed fasteners, seams, sealant/tape, or flashing. Installer error also includes a lack of attention to detail when it comes to manufacturer recommendations.
Many roofers offer a warranty, but no one covers leaks through the roof. They also do not typically cover when screws start backing out , this can include hundreds and thousands of screws. At ACR1, we can roof over your metal roof and provide a 20-year leak through warranty. In some cases, the only way to fix your leaky roof is to pull the old roof off and replace it, which is typically three times the cost of a roof-over service.
Oil Canning on Metal Roofs
Oil canning is a common issue that affects commercial metal roofs. It is caused by metal panels that are not properly secured, leading to small waves and wrinkles in the metal. This can be caused by improper panel installation or standing water on a flat roof.
These wrinkles can be unsightly and may even lead to leaks in some cases. For this reason, it is important to ensure that the company doing your metal reroofing project is experienced and knowledgeable in how to properly secure metal panels, as well as how to detect oil canning early on before it has a chance to cause more serious damage.
In addition, oil canning may also be caused by thermal expansion and contraction, which occurs when temperatures change from hot to cold or vice versa. Proper insulation around the perimeter of the building should help reduce this type of movement. Additionally, some metal panel materials are less prone to oil canning than others; for example, steel typically experiences more oil-canning effects than aluminum. As such, one should take into account the material being used when selecting a product for their re-roofing project.
Finally, proper maintenance of your metal roof will also help reduce the chances of developing oil-canning issues over time. Depending on the type of metal panel installed, regular inspection and cleaning may be necessary in order to avoid potential problems down the road. If you notice any signs of oil canning while inspecting your roof, it’s best to call in a professional right away in order to address any potential issues before they become bigger problems later on.
Corrosion on Metal Roofs
Corrosion is another issue that may arise if proper maintenance isn’t performed on a regular basis – especially in older commercial buildings where ventilation may not have been adequate when initially installing the roof system.
Corrosion happens when oxygen combines with certain metals such as steel and iron that are exposed during installation or repairs; this causes oxidation which leads to corrosion over time without proper protection being applied in order to fight off rust development and deterioration of the materials being used for your roof system.
The best way to prevent corrosion is by applying rust inhibitor treatments whenever possible during installation or repairs; additionally, keeping surfaces clean of debris will also reduce any chances of oxidation buildup leading up to extensive rust formation down the road.
Furthermore, if you live in an area with high humidity, periodic inspections are essential to spot any signs of corrosion before it becomes a serious issue.
Scratching and Scuffing on Metal Roofs
Scratching and scuffing are common issues that can arise with metal roofs. Foot traffic, tools, ladders, and other items can lead to scratches or dents in the panels. It is important to take preventive measures when walking on a metal roof. Wear protective shoes or use plywood boards for extra protection.
In addition, you should inspect your roof regularly for any signs of scratching or scuffing – especially in areas where foot traffic occurs often, such as walkways and access points. If necessary, repair these areas immediately or have them inspected by a professional if they are not easily visible from the ground.
Scratches and scuffs can also be caused by improper handling during shipping or installation. If the metal was improperly could or recoiled, it can strip the coating, and a lack of edge guard during shipping can also cause damage. Additionally, If tools are dropped or rubbed on the metal sheets, or they are walked on by the contractors, they can become damaged. If you notice damage that you think was a result of improper installation, contact your roofing contractor.
Many scratches and scuffs can be fixed with paint, but if the scratch goes down to the core of the steel, it will need to be replaced to ensure the roof remains structurally sound.
Reducing Metal Roofing Risks
In order to reduce these risks, all underlying problems related to structural integrity should be addressed before any reroofing project begins. If there are issues such as sagging joists or warped decking, these should be repaired before attempting to install a new layer of material.
Additionally, any existing fasteners or seams should be inspected and sealed if necessary. Finally, it is also important to ensure that the new roofing material is properly applied so as to create an air-tight seal between the two layers.
By taking the time to address any underlying issues associated with reroofing over a commercial metal roof, you can help reduce the risk of damage and prolong the life of your structure. If you are still unsure whether this project is right for you, consult a professional who can provide advice on the best course of action.
Although reroofing over an existing metal roof can be a cost-effective solution, it is important to be aware of the potential risks involved. By doing your research and taking the necessary precautions before beginning the project, you can help ensure that your roof lasts for years to come.
Contact the experts at ACR1 Commercial Roofing to learn more about your commercial roofing options.
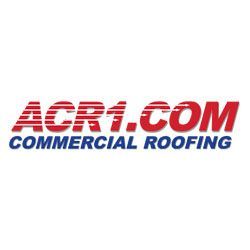
Author:
Floyd Mason
Born and raised in farming in Iowa
Worked in and around construction since 1977
BS in Corporate Finance and Financial & Estate Planning from Brigham Young University. Involved in Boy Scouts of America for more than 35 years, Scoutmaster 15 years Estimator, Project Manager, Sales Representative, Crew Leader, Laborer, Territory Manager, District Manager, Regional Manager, National Sales Manager,
ACR1.COM Sales & Marketing Manager since 2013.
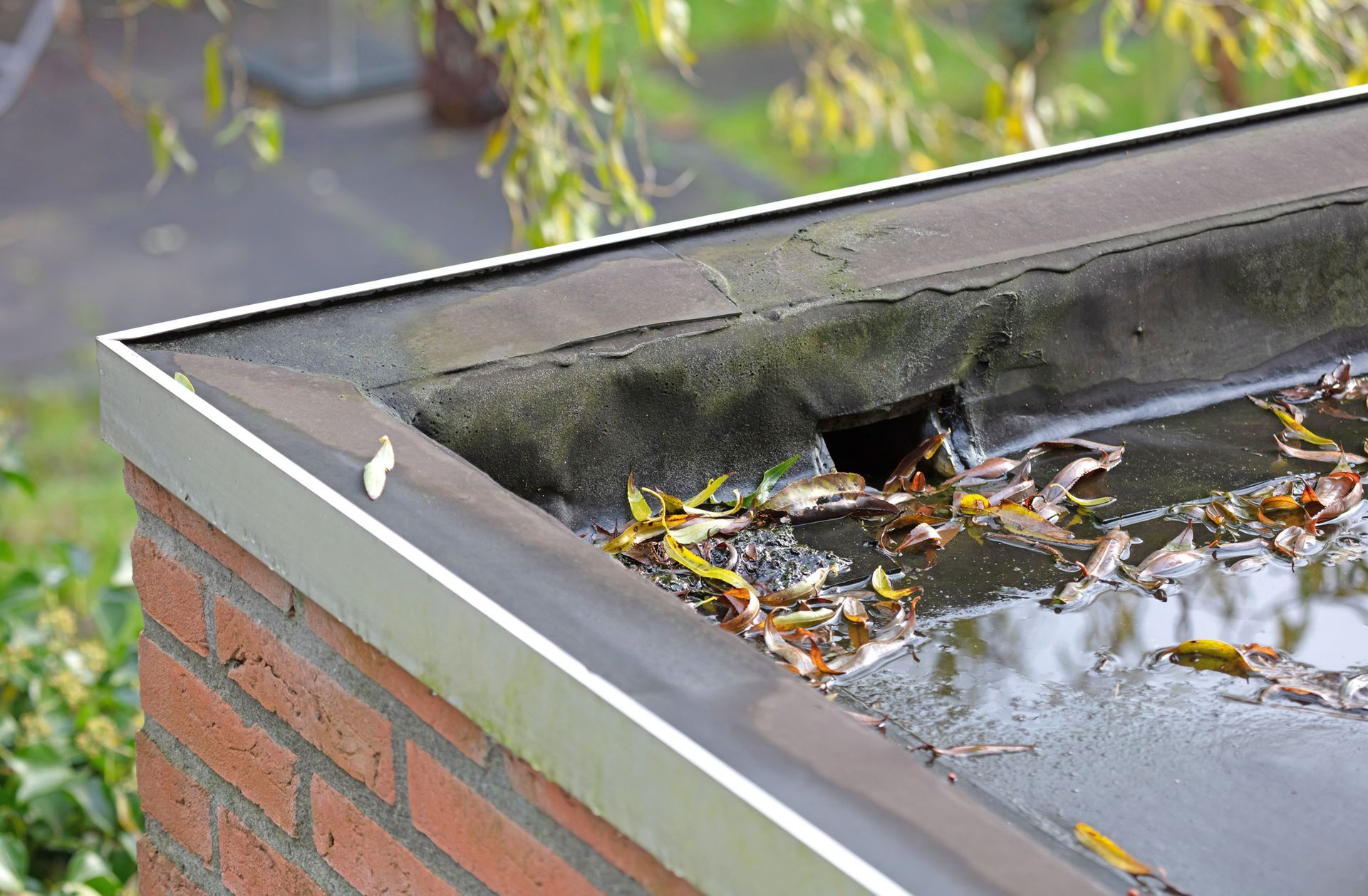